Bremsenlabor von Bosch
Besuch beim Bäcker der Bremsbeläge
17. Dezember 2024 agvs-upsa.ch – Bremsen bremsen halt? So simpel ist es nicht: Bremsbeläge sind eine unterschätzte Autokomponente. In jedem Aftermarket-Bremsbelag stecken Jahre der Entwicklung – und manchmal gar Buchenholz. Exklusiv besuchen wir das Bremsenlabor von Bosch, global die Nummer eins bei Bremsbelägen. Timothy Pfannkuchen
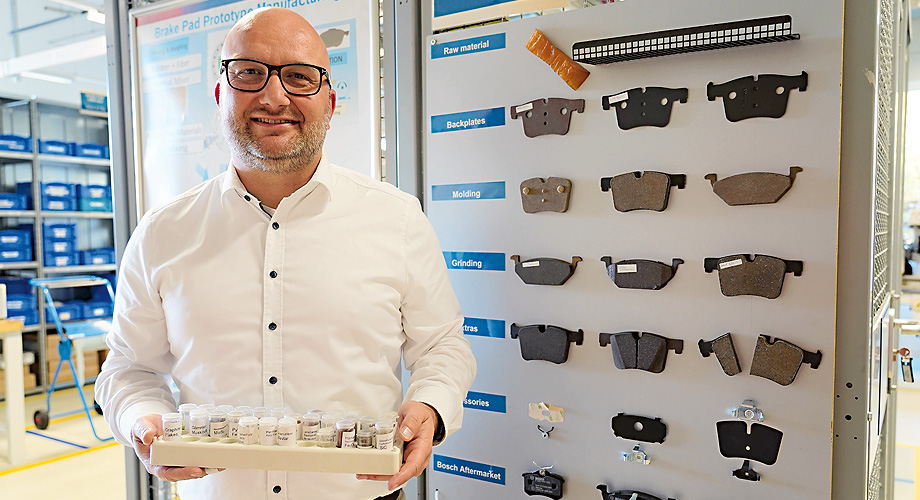
Wo 10 000 Bremsbelagstypen entstehen: Im Bosch-Bremsenlabor erläutert Andreas Mayer, Produktgebietsleiter Aftermarket-Bremsen, die Prozesse. Und zeigt einige mögliche der 15 bis 25 Inhaltsstoffe eines Vremsbelags. Einer davon ist zum Beispiel Buchenholz. Foto: AGVS-Medien
Ihren Ausweis, bitte: Vor dem Einlass in Boschs Aftermarket-Epizentrum im deutschen Karlsruhe sind erst mal die Hürden des Werkschutzes zu überwinden. Freundlich und im badischen Zungenschlag werden wir identifiziert, fotografiert, geschult und unterschreiben allerlei Papiere. In denen steht: alles geheim hier. Dass wir trotzdem hinein und – bitte stets nach Rücksprache – gar Fotos machen dürfen, ist eine exklusive Ausnahme. Denn wir besuchen, was man eigentlich nicht besuchen kann: das Bremsenlabor von Bosch.
Das Bremsenlabor duckt sich in den Schatten des Aftermarket-Zentrallagers und trägt architektonisch den Charme einer Primarschule aus den 1970er-Jahren. Irgendwie ist auch das sehr Robert Bosch GmbH: Sein statt Schein; in dem unscheinbaren einstöckigen Gebäude haben sie es faustdick hinter den technologischen Ohren. Gestatten, Andreas Mayer. Fester Händedruck und die feste Überzeugung, dass Bremsen viel mehr ist als Verzögern. Mayers offizieller Funktionstitel lautet «Product Area Owner (VP)». Aha. «Produktgebietsleiter Aftermarket-Bremsen», erklärt Mayer schmunzelnd. Kurz: Mayer ist der Chef. Und wie auffällig viele hier ein echter «Boschianer »: Praktikum, Diplomarbeit, Karriere – 20 Dienstjahre. Den ortsüblichen Dialekt hat der gebürtige Hannoveraner nicht adaptiert, aber die ortsübliche Haltung: Wenn Bosch was macht, dann richtig.
Weltpremieren haben Tradition
«Lieber Geld verlieren als Vertrauen.» So hatte das einst Robert Bosch (1861 bis 1942) formuliert. Und gründete 1886, im Geburtsjahr des Autos, jenes Unternehmen, das sich dieses Vertrauen mit Qualität verdiente – und mit Innovationen. Servobremse (1927), elektronischesABS (1978), das darauf basierende ESP (1995): alles Bosch-Weltpremieren. Heute ist Bosch weltweit grösster Autozulieferer und zum Beispiel Nummer eins bei ABS-Systemen. Verblüffend: Bei Bremsbelägen (auf die wir uns hier fokussieren) ist Bosch kein Erstausrüster. Wohl aber global führend bei Aftermarket-Bremsbelägen und in Europa auch bei Bremsscheiben. Das Aftermarket-Programm umfasst 46 000 Bremsenartikel. Darunter dutzende Flüssigkeiten wie etwa das neue DOT 4 E, eine Universal- Bremsflüssigkeit ohne gesundheitsschädliche Borate und darum kein Gefahrgut mehr. Oder 10 000 Bremsbelagstypen, die 97 Prozent des Marktes abdecken. Damit das so bleibt, gibt es drei Bremsenlabore mit 120 Mitarbeitenden: in China, den USA und am Aftermarket-Stammsitz im deutschen Karlsruhe.
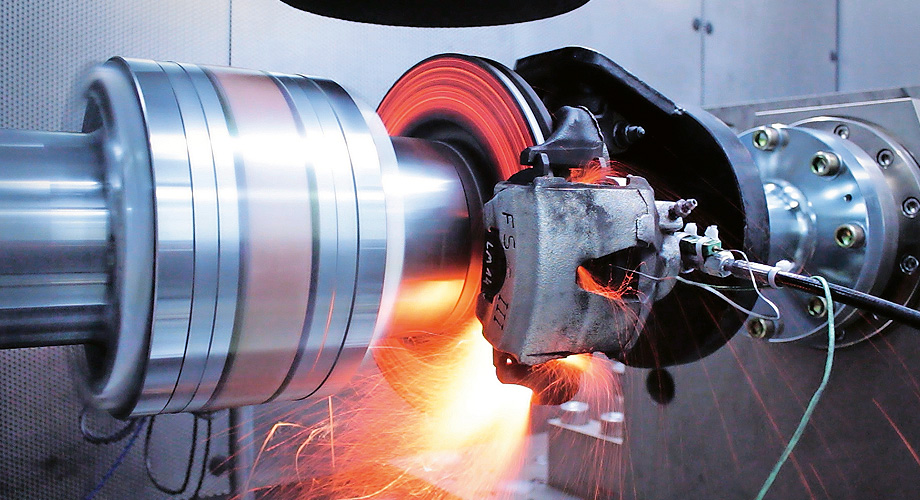
Testen, bis wortwörtlich die Bremsscheiben glühen: Im Bremsenlabor werden Scheiben und Beläge etlichen Tests unterzogen, ehe es danach noch on the Road zum Realversuch geht. Getestet werden zum Beispiel die Abscherfestigkeit der Beläge, Vibrationen und natürlich die Reib-, also die Verzögerungswerte. Foto: Bosch
In der Küche Bremsbeläge backen
«Es ist ein bisschen wie Kochen: Am Anfang stehen die Zutaten», sagt der 46-jährige Mayer augenzwinkernd und führt uns ins Labor. Tiegel und Töpfe, wissenschaftliches Gerät: Hier wird analysiert, experimentiert, komponiert. Eine Küche, in der Mayers Team neue Bremsbeläge abschmeckt. Ist der Bremsbelag denn nicht längst zu Ende entwickelt? Mayer schaut kurz, als hätten wir etwas Unanständiges gefragt, und antwortet: «Würden wir aufhören, wären wir nach drei Jahren vom Markt. Die Bremse ist ein unterschätztes Bauteil. Ein Bremsbelag besteht aus 15 bis 25 Materialien, und natürlich verbessern wir fortlaufend.» Was steckt denn da drin? Metalle wie Eisen oder Messing, unaussprechliche Dinge wie Molybdänsulfid, häufig Aramid, Grafit, Kevlar, dazu Fasern aus Glasoder Gummi und sozusagen als Klebstoff Kunst- und Naturharze. «Und manchmal Buchenholz », sagt Bremsbelagbäcker Mayer, schmunzelt und geniesst unsere Verblüffung. Holz kann die Kompressibilität trimmen. Heisst: Treten wir ins Pedal, muss der vermeintlich betonharte Belag eine Winzigkeit komprimierbar sein. Ist er zu hart, quietscht es. Darf es nicht, findet Mayer, «im leisen Elektroauto schon gar nicht. Quietschen beeinträchtigt nicht die Funktion, aber stört die Endkundinnen und -kunden. Das entspräche nicht unserem Selbstverständnis». Also einfach weiche Beläge? Ist der Belag zu weich, wird unser Fussgefühl schwammig. «Es muss sich gut anfühlen, und Europäer lieben ihre Bremse bissig», erklärt Mayer. Womit wir den Zielkonflikt zu verstehen beginnen: jeder Belag eine Quadratur des Bremsenkreises. Ist der ideale Kompromiss gefunden, ist Mayers Team aber nicht fertig: Für Amerika zum Beispiel ist ein weiches Pedalgefühl gefragt. Ganz abgesehen von gesetzlichen Bestimmungen: In Europa wird erwartet, dass irgendwann eine Vorschrift kommt, dass Beläge kupferfrei sein müssen. Die USA fordern das längst – und damals war Bosch der erste Anbieter, der es erfüllte. Seither ist jeder Bosch-Belag kupferfrei und parat für eine vermutlich folgende entsprechende EU-Regel.
Nein, an Aufgaben fehlt es hier nie. Jede neue Charge eines Rohstoffs wird auf seine Zusammensetzung geprüft und jedes Produktionslos getestet – was bei populären Belägen monatliche Prüfung heisst. Mayer erzählt sowas sympathisch locker und ist quasi eine lebende Bremsenenzyklopädie. Manchmal rutscht ihm statt «unsere Bremsen» sogar «meine Bremsen» heraus. Bremsen nehmen sie bei Bosch halt persönlich.
Vom Labor in die Backstube
Im Raum nebenan schiebt ein Mitarbeiter frische Bremsbeläge in einen Backofen wie ein Konditor seine Guetzli. «Wie gesagt, wie Kochen », sagt Mayer lachend, «im Labor rühren wir den Teig an, hier backen wir unter Druck und Hitze den Bremsbelag unter denselben Bedingungen wie später in der Serienproduktion. » Ein Raum weiter: die Folterkammer. Hier wird das Backwerk belastet, bis es im Wortsinn kracht. Etwa im Test auf Abscherfestigkeit: Wie gut hält der Belag auf der Trägerplatte? Schmeckt das Ergebnis, wandert das Bremsenmenü in die Halle mit gekapselten Prüfständen im Format von Überseecontainern. Im Kontrollraum flimmern Kurven und Zahlen über die Monitore, zeigen Thermobilder die Temperaturen auf mit 600 bis 800 Grad glühenden Bremsscheiben, während im Prüfstand selbst Klimata von Arktis bis Wüste und etliche Fahrzyklen bis hinauf zu 250 Sachen die Bremsen stressen. In Hochregalen liegen Achsen wie bei Ikea die Billy-Regale. Wieso wird denn komplett mit Radaufhängungen getestet? «Wir müssen für jeden Fahrzeugtyp nachweisen, dass der Bremsbelag für genau dieses Fahrzeug alle gesetzlichen Bestimmungen wie die ECE R90 erfüllt. Und natürlich unsere eigenen Standards, die noch deutlich über die gesetzlichen Anforderungen hinausgehen », sagt Mayer. Zwei Beispiele: Vibrationen sind gesetzlich ebenso ungeregelt wie Fading oder wie lange Beläge im Alltag halten sollen. Also stellt Bosch eigene Regeln dafür auf, Übererfüllung lautet das Ziel.
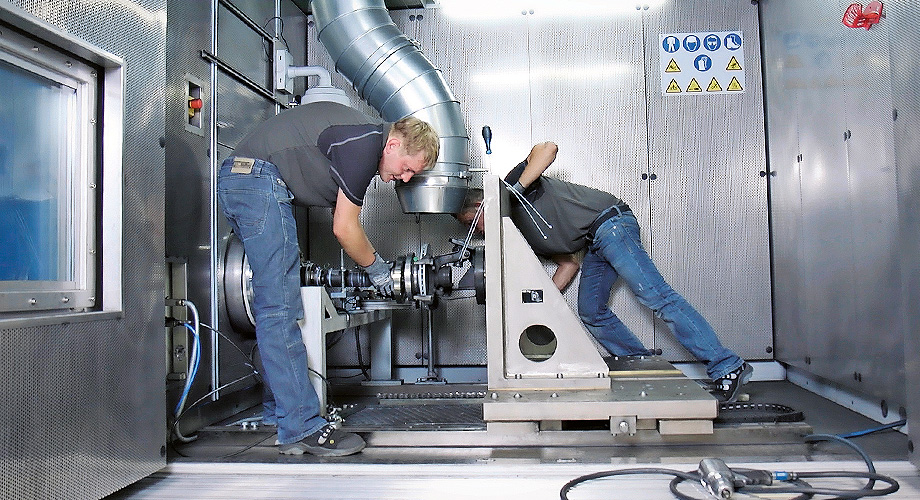
Detailtreue: Je nach Test werden zum Teil komplette Achsen mit Dämpfern und Co. in Prüfständen verbaut. Denn jedes Aftermarket- Bremsenteil muss genau für das spezifische Fahrzeug geeignet sein. Foto: Bosch
Euro 7 und der Bremsstaub
Selbst die Abluft der Prüfstände wird analysiert. «Euro 7», sagt Mayer lakonisch: Voraussichtlich 2027 sind scharfe Grenzwerte für Bremsabrieb vorgesehen. Bekommt die Bremsenbranche das hin? Mayer verkneift sich jeden Seitenhieb auf Wettbewerber und sagt diplomatisch «Es gibt Beläge, die das können. Man muss einfach früh genug damit anfangen. Unsere Beläge können es.» Nerven neue Regularien? «Nein, wir sehen uns da in der Verantwortung. Deshalb sind wir auch in den Arbeitsgruppen dabei, welche die Testverfahren definieren.» Ironischerweise, fügt Mayer an, sei Bremsstaub in den USA bereits viel länger ein Thema. Nur nicht aus Umweltgründen: US-Kunden hassen nichts mehr als dreckige Felgen am glänzenden Gefährt.
Härtetests in den Alpen
Damit ist unser Rundgang beendet. Und für die Beläge die Tests? «Keineswegs», betont Mayer und deutet nach draussen, wo die Wagenflotte vom VW Polo bis zum Mercedes Sprinter bereitsteht, um auszurücken auf die Schwäbische Alb, den Grossglockner oder den Stelvio – weil die Realität immer noch viel gemeinere Martern erdenkt als jeder Prüfstand. «Im Strassentest behandeln wir die Bremsen so, wie man sie nicht behandeln sollte. Und es muss sich einfach gut anfühlen. Dieser subjektive Teil lässt sich nicht in Zahlen fassen», so Mayer. Wenn Beläge, Scheiben und Co. dies meistern, folgt die Freigabe der Serienproduktion (die in vier Fünftel der Bremsbelagsfälle Bosch selbst übernimmt). Und wenn nicht oder wenn nur bei einem der vielen Tests die Bremse ein einziges Mal nicht gut bremst? Geht alles von vorne los.
Wie lange dauert das Ganze eigentlich? «Meistens um die drei Jahre.» Lohnt sich das? Offensichtlich: Vor einiger Zeit führte die EU mal Stichproben durch. Dabei fiel fast die Hälfte der Beläge durch, weil sie die gesetzlichen Mindestanforderungen nicht erfüllten. «Unsere waren nicht dabei», sagt Mayer und sieht zufrieden aus. Kein Wunder, ist hier alles geheim: Hier käme die Konkurrenz gerne mal gucken. Denn bei Bosch brennen sie für ihre Bremsen. Robert Bosch hätte das Bremsenlabor sicher gut gefallen.
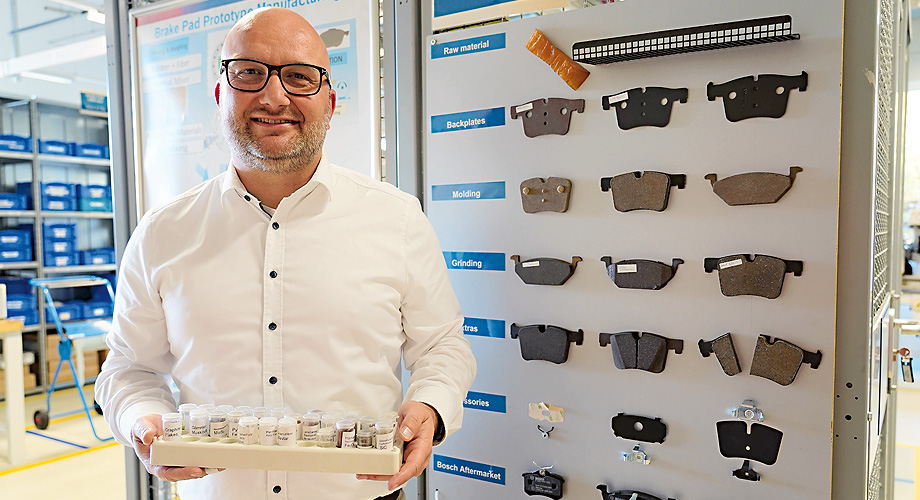
Wo 10 000 Bremsbelagstypen entstehen: Im Bosch-Bremsenlabor erläutert Andreas Mayer, Produktgebietsleiter Aftermarket-Bremsen, die Prozesse. Und zeigt einige mögliche der 15 bis 25 Inhaltsstoffe eines Vremsbelags. Einer davon ist zum Beispiel Buchenholz. Foto: AGVS-Medien
Ihren Ausweis, bitte: Vor dem Einlass in Boschs Aftermarket-Epizentrum im deutschen Karlsruhe sind erst mal die Hürden des Werkschutzes zu überwinden. Freundlich und im badischen Zungenschlag werden wir identifiziert, fotografiert, geschult und unterschreiben allerlei Papiere. In denen steht: alles geheim hier. Dass wir trotzdem hinein und – bitte stets nach Rücksprache – gar Fotos machen dürfen, ist eine exklusive Ausnahme. Denn wir besuchen, was man eigentlich nicht besuchen kann: das Bremsenlabor von Bosch.
Das Bremsenlabor duckt sich in den Schatten des Aftermarket-Zentrallagers und trägt architektonisch den Charme einer Primarschule aus den 1970er-Jahren. Irgendwie ist auch das sehr Robert Bosch GmbH: Sein statt Schein; in dem unscheinbaren einstöckigen Gebäude haben sie es faustdick hinter den technologischen Ohren. Gestatten, Andreas Mayer. Fester Händedruck und die feste Überzeugung, dass Bremsen viel mehr ist als Verzögern. Mayers offizieller Funktionstitel lautet «Product Area Owner (VP)». Aha. «Produktgebietsleiter Aftermarket-Bremsen», erklärt Mayer schmunzelnd. Kurz: Mayer ist der Chef. Und wie auffällig viele hier ein echter «Boschianer »: Praktikum, Diplomarbeit, Karriere – 20 Dienstjahre. Den ortsüblichen Dialekt hat der gebürtige Hannoveraner nicht adaptiert, aber die ortsübliche Haltung: Wenn Bosch was macht, dann richtig.
Weltpremieren haben Tradition
«Lieber Geld verlieren als Vertrauen.» So hatte das einst Robert Bosch (1861 bis 1942) formuliert. Und gründete 1886, im Geburtsjahr des Autos, jenes Unternehmen, das sich dieses Vertrauen mit Qualität verdiente – und mit Innovationen. Servobremse (1927), elektronischesABS (1978), das darauf basierende ESP (1995): alles Bosch-Weltpremieren. Heute ist Bosch weltweit grösster Autozulieferer und zum Beispiel Nummer eins bei ABS-Systemen. Verblüffend: Bei Bremsbelägen (auf die wir uns hier fokussieren) ist Bosch kein Erstausrüster. Wohl aber global führend bei Aftermarket-Bremsbelägen und in Europa auch bei Bremsscheiben. Das Aftermarket-Programm umfasst 46 000 Bremsenartikel. Darunter dutzende Flüssigkeiten wie etwa das neue DOT 4 E, eine Universal- Bremsflüssigkeit ohne gesundheitsschädliche Borate und darum kein Gefahrgut mehr. Oder 10 000 Bremsbelagstypen, die 97 Prozent des Marktes abdecken. Damit das so bleibt, gibt es drei Bremsenlabore mit 120 Mitarbeitenden: in China, den USA und am Aftermarket-Stammsitz im deutschen Karlsruhe.
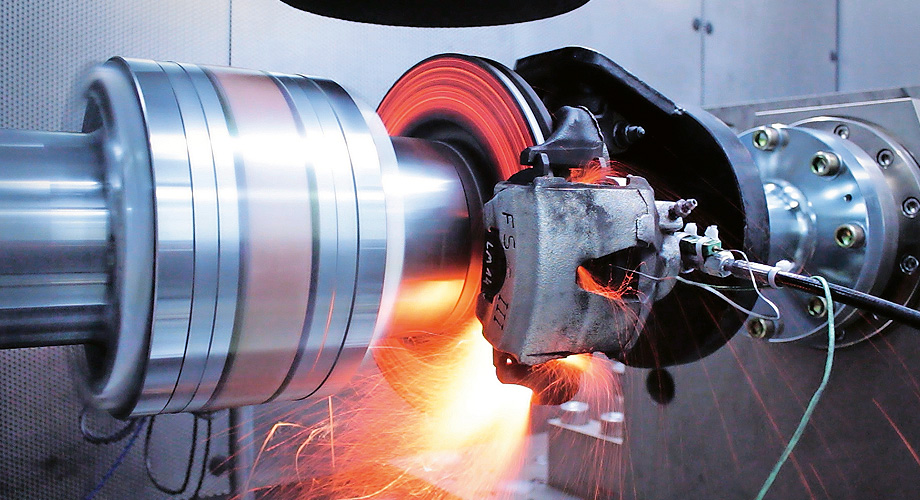
Testen, bis wortwörtlich die Bremsscheiben glühen: Im Bremsenlabor werden Scheiben und Beläge etlichen Tests unterzogen, ehe es danach noch on the Road zum Realversuch geht. Getestet werden zum Beispiel die Abscherfestigkeit der Beläge, Vibrationen und natürlich die Reib-, also die Verzögerungswerte. Foto: Bosch
In der Küche Bremsbeläge backen
«Es ist ein bisschen wie Kochen: Am Anfang stehen die Zutaten», sagt der 46-jährige Mayer augenzwinkernd und führt uns ins Labor. Tiegel und Töpfe, wissenschaftliches Gerät: Hier wird analysiert, experimentiert, komponiert. Eine Küche, in der Mayers Team neue Bremsbeläge abschmeckt. Ist der Bremsbelag denn nicht längst zu Ende entwickelt? Mayer schaut kurz, als hätten wir etwas Unanständiges gefragt, und antwortet: «Würden wir aufhören, wären wir nach drei Jahren vom Markt. Die Bremse ist ein unterschätztes Bauteil. Ein Bremsbelag besteht aus 15 bis 25 Materialien, und natürlich verbessern wir fortlaufend.» Was steckt denn da drin? Metalle wie Eisen oder Messing, unaussprechliche Dinge wie Molybdänsulfid, häufig Aramid, Grafit, Kevlar, dazu Fasern aus Glasoder Gummi und sozusagen als Klebstoff Kunst- und Naturharze. «Und manchmal Buchenholz », sagt Bremsbelagbäcker Mayer, schmunzelt und geniesst unsere Verblüffung. Holz kann die Kompressibilität trimmen. Heisst: Treten wir ins Pedal, muss der vermeintlich betonharte Belag eine Winzigkeit komprimierbar sein. Ist er zu hart, quietscht es. Darf es nicht, findet Mayer, «im leisen Elektroauto schon gar nicht. Quietschen beeinträchtigt nicht die Funktion, aber stört die Endkundinnen und -kunden. Das entspräche nicht unserem Selbstverständnis». Also einfach weiche Beläge? Ist der Belag zu weich, wird unser Fussgefühl schwammig. «Es muss sich gut anfühlen, und Europäer lieben ihre Bremse bissig», erklärt Mayer. Womit wir den Zielkonflikt zu verstehen beginnen: jeder Belag eine Quadratur des Bremsenkreises. Ist der ideale Kompromiss gefunden, ist Mayers Team aber nicht fertig: Für Amerika zum Beispiel ist ein weiches Pedalgefühl gefragt. Ganz abgesehen von gesetzlichen Bestimmungen: In Europa wird erwartet, dass irgendwann eine Vorschrift kommt, dass Beläge kupferfrei sein müssen. Die USA fordern das längst – und damals war Bosch der erste Anbieter, der es erfüllte. Seither ist jeder Bosch-Belag kupferfrei und parat für eine vermutlich folgende entsprechende EU-Regel.
Nein, an Aufgaben fehlt es hier nie. Jede neue Charge eines Rohstoffs wird auf seine Zusammensetzung geprüft und jedes Produktionslos getestet – was bei populären Belägen monatliche Prüfung heisst. Mayer erzählt sowas sympathisch locker und ist quasi eine lebende Bremsenenzyklopädie. Manchmal rutscht ihm statt «unsere Bremsen» sogar «meine Bremsen» heraus. Bremsen nehmen sie bei Bosch halt persönlich.
Vom Labor in die Backstube
Im Raum nebenan schiebt ein Mitarbeiter frische Bremsbeläge in einen Backofen wie ein Konditor seine Guetzli. «Wie gesagt, wie Kochen », sagt Mayer lachend, «im Labor rühren wir den Teig an, hier backen wir unter Druck und Hitze den Bremsbelag unter denselben Bedingungen wie später in der Serienproduktion. » Ein Raum weiter: die Folterkammer. Hier wird das Backwerk belastet, bis es im Wortsinn kracht. Etwa im Test auf Abscherfestigkeit: Wie gut hält der Belag auf der Trägerplatte? Schmeckt das Ergebnis, wandert das Bremsenmenü in die Halle mit gekapselten Prüfständen im Format von Überseecontainern. Im Kontrollraum flimmern Kurven und Zahlen über die Monitore, zeigen Thermobilder die Temperaturen auf mit 600 bis 800 Grad glühenden Bremsscheiben, während im Prüfstand selbst Klimata von Arktis bis Wüste und etliche Fahrzyklen bis hinauf zu 250 Sachen die Bremsen stressen. In Hochregalen liegen Achsen wie bei Ikea die Billy-Regale. Wieso wird denn komplett mit Radaufhängungen getestet? «Wir müssen für jeden Fahrzeugtyp nachweisen, dass der Bremsbelag für genau dieses Fahrzeug alle gesetzlichen Bestimmungen wie die ECE R90 erfüllt. Und natürlich unsere eigenen Standards, die noch deutlich über die gesetzlichen Anforderungen hinausgehen », sagt Mayer. Zwei Beispiele: Vibrationen sind gesetzlich ebenso ungeregelt wie Fading oder wie lange Beläge im Alltag halten sollen. Also stellt Bosch eigene Regeln dafür auf, Übererfüllung lautet das Ziel.
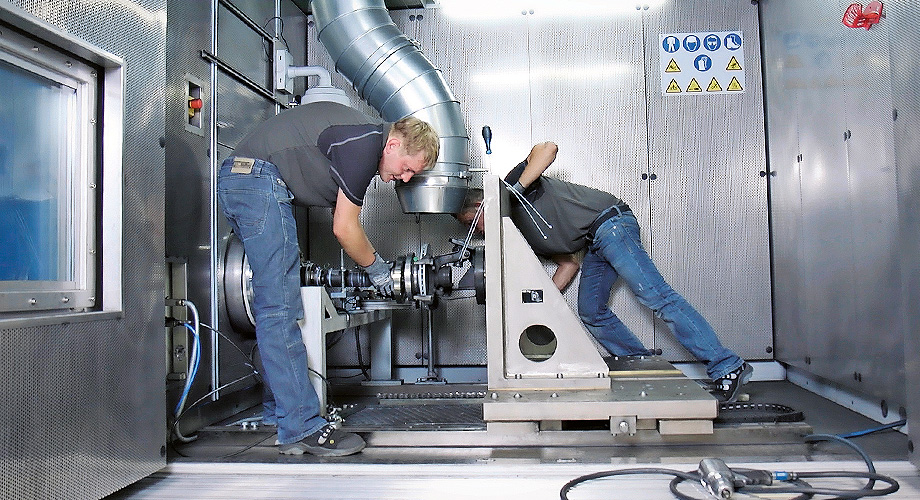
Detailtreue: Je nach Test werden zum Teil komplette Achsen mit Dämpfern und Co. in Prüfständen verbaut. Denn jedes Aftermarket- Bremsenteil muss genau für das spezifische Fahrzeug geeignet sein. Foto: Bosch
Euro 7 und der Bremsstaub
Selbst die Abluft der Prüfstände wird analysiert. «Euro 7», sagt Mayer lakonisch: Voraussichtlich 2027 sind scharfe Grenzwerte für Bremsabrieb vorgesehen. Bekommt die Bremsenbranche das hin? Mayer verkneift sich jeden Seitenhieb auf Wettbewerber und sagt diplomatisch «Es gibt Beläge, die das können. Man muss einfach früh genug damit anfangen. Unsere Beläge können es.» Nerven neue Regularien? «Nein, wir sehen uns da in der Verantwortung. Deshalb sind wir auch in den Arbeitsgruppen dabei, welche die Testverfahren definieren.» Ironischerweise, fügt Mayer an, sei Bremsstaub in den USA bereits viel länger ein Thema. Nur nicht aus Umweltgründen: US-Kunden hassen nichts mehr als dreckige Felgen am glänzenden Gefährt.
Härtetests in den Alpen
Damit ist unser Rundgang beendet. Und für die Beläge die Tests? «Keineswegs», betont Mayer und deutet nach draussen, wo die Wagenflotte vom VW Polo bis zum Mercedes Sprinter bereitsteht, um auszurücken auf die Schwäbische Alb, den Grossglockner oder den Stelvio – weil die Realität immer noch viel gemeinere Martern erdenkt als jeder Prüfstand. «Im Strassentest behandeln wir die Bremsen so, wie man sie nicht behandeln sollte. Und es muss sich einfach gut anfühlen. Dieser subjektive Teil lässt sich nicht in Zahlen fassen», so Mayer. Wenn Beläge, Scheiben und Co. dies meistern, folgt die Freigabe der Serienproduktion (die in vier Fünftel der Bremsbelagsfälle Bosch selbst übernimmt). Und wenn nicht oder wenn nur bei einem der vielen Tests die Bremse ein einziges Mal nicht gut bremst? Geht alles von vorne los.
Wie lange dauert das Ganze eigentlich? «Meistens um die drei Jahre.» Lohnt sich das? Offensichtlich: Vor einiger Zeit führte die EU mal Stichproben durch. Dabei fiel fast die Hälfte der Beläge durch, weil sie die gesetzlichen Mindestanforderungen nicht erfüllten. «Unsere waren nicht dabei», sagt Mayer und sieht zufrieden aus. Kein Wunder, ist hier alles geheim: Hier käme die Konkurrenz gerne mal gucken. Denn bei Bosch brennen sie für ihre Bremsen. Robert Bosch hätte das Bremsenlabor sicher gut gefallen.
Kommentar hinzufügen
Kommentare